Have You Seen How an Alabama Robotics Engineering Company Handles Complex Material Stacking for Logistics?
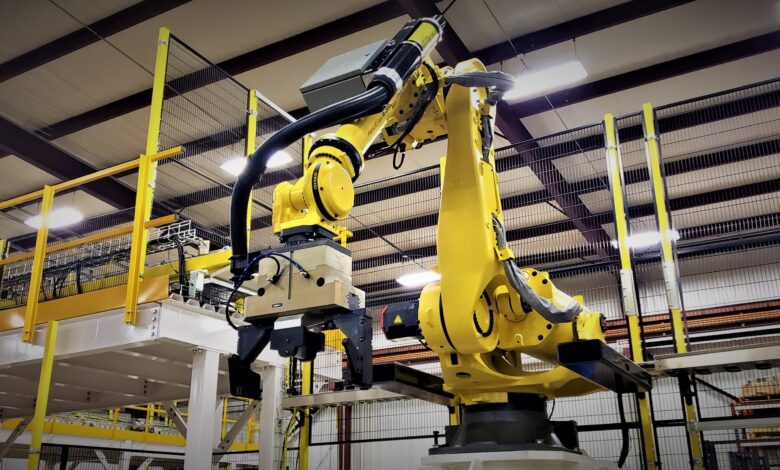
In the fast-moving world of logistics, keeping materials stacked properly isn’t as simple as it sounds. Precision, speed, and efficiency all play a role in ensuring smooth operations.
An Alabama robotics engineering company is changing the game by designing intelligent robotic systems that handle complex material stacking with unmatched accuracy.
High-Speed Sorting Algorithms That Maximize Efficiency in Fast-Paced Logistics Environments
Logistics operations depend on speed, and any delay in sorting materials can create bottlenecks that slow down the entire supply chain. A robotics engineering company in Alabama uses advanced sorting algorithms that analyze incoming loads in real-time, determining the best placement for each item.
This level of automation eliminates guesswork, ensuring materials are stacked efficiently and in the correct sequence for easy retrieval.
These high-speed sorting algorithms optimize every movement, minimizing the time it takes for robotic arms to pick, place, and stack materials. Unlike manual stacking, which is prone to human error and inefficiencies, automated systems handle large volumes with remarkable precision.
Whether it’s organizing pallets in a warehouse or preparing shipments for transport, these intelligent algorithms help businesses keep up with demand without unnecessary slowdowns.
Collision Avoidance Systems That Keep Stacking Operations Smooth and Accident-Free
Stacking heavy or delicate materials comes with risks, especially in high-traffic logistics facilities. Without proper coordination, collisions between machinery, pallets, or storage racks can lead to costly damages and downtime.
An Alabama robotics engineering company integrates collision avoidance systems into its automation solutions to prevent accidents before they happen.
These systems rely on sensors and real-time monitoring to detect potential obstacles in the stacking environment. If a robotic arm or automated forklift senses an obstruction, it adjusts its movement instantly, avoiding crashes while continuing operations.
This level of intelligence allows logistics centers to operate efficiently while significantly reducing damage to inventory and equipment. By prioritizing safety, these robotics systems improve both productivity and workplace conditions.
Custom Stacking Configurations That Adjust to Space Constraints and Load Requirements
Not all storage spaces are created equal, and logistics facilities often face challenges when it comes to organizing materials efficiently. Traditional stacking methods rely on fixed patterns, but a robotics engineering company in Alabama develops solutions that adapt to different layouts and load requirements.
This flexibility allows warehouses to make the most of their available space without compromising stability or accessibility.
These robotic stacking systems analyze the dimensions, weight, and fragility of materials before determining the best way to arrange them. Whether stacking oddly shaped packages, fragile goods, or bulk inventory, these robots can configure stacks in a way that maximizes space while ensuring easy access for retrieval.
The result is a streamlined operation that reduces wasted storage areas and improves inventory management.
Conveyor Coordination That Ensures Seamless Material Flow from One Process to Another
A well-coordinated conveyor system is the backbone of any efficient logistics operation. If materials don’t transition smoothly from one stage to the next, it can lead to delays, congestion, and increased handling time.
A robotics engineering company in Alabama specializes in designing robotic stacking systems that work seamlessly with conveyor belts, ensuring a continuous flow of materials.
These systems use synchronized movement to transfer materials between conveyors and stacking zones without interruption. By automating this process, companies eliminate unnecessary stops and reduce labor-intensive handling.
This level of precision prevents slowdowns, keeping operations moving at full speed while improving overall efficiency.
Gripper Technology That Handles Fragile and Heavy Materials Without Damage
Material stacking requires more than just speed—it demands the right touch. Heavy loads need a firm grip, while fragile items require delicate handling to prevent breakage.
A robotics engineering company in Alabama develops advanced gripper technology that adjusts pressure based on the type of material being stacked.
These robotic grippers use sensors to detect weight, shape, and surface texture, allowing them to apply the perfect amount of force for each item. Whether handling glass, electronic components, or bulk goods, these systems ensure materials are stacked securely without risk of damage.
By combining strength with precision, these robotic solutions make logistics handling more reliable than ever.