The Key Differences Between Welded Steel and Modular Aluminum Framing for Workstations
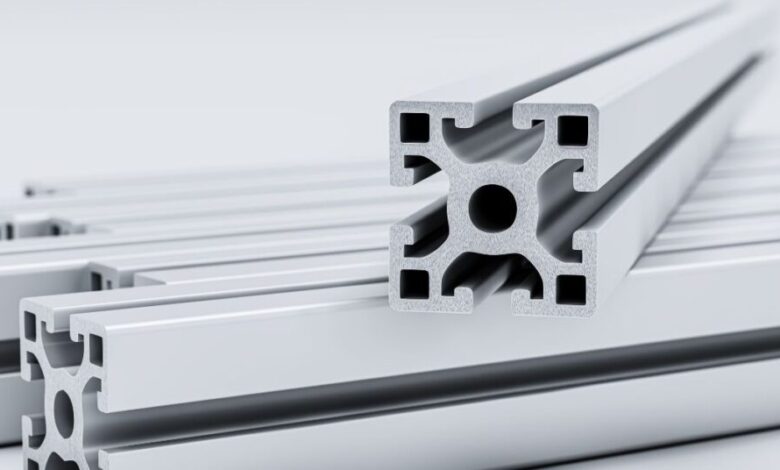
Choosing the right workstation framing can make a huge difference in efficiency, durability, and flexibility. Welded steel and modular aluminum framing are two popular options, each with its own advantages depending on the work environment.
Understanding their key differences helps businesses and manufacturers select the best solution for their needs.
Structural Strength and Load Capacity in Demanding Work Environments
Workstations in industrial settings must withstand heavy equipment, constant movement, and intense workloads. Welded steel is known for its impressive strength and ability to support significant weight without flexing.
It’s ideal for applications where stability is a priority, such as machining stations or assembly lines handling large components. Once welded, steel creates a permanent, rigid structure that won’t shift under pressure, making it the go-to option for high-load environments.
On the other hand, aluminum framing offers a strong yet lightweight alternative. While not as dense as steel, it provides excellent load-bearing capacity when properly designed. It distributes weight efficiently, making it a reliable choice for workstations that need to support equipment but also require adjustability.
For environments that don’t demand extreme weight resistance, aluminum framing provides ample strength while offering more flexibility for future modifications.
Material Fatigue and Long-Term Durability Under Repetitive Use
Over time, materials undergo stress from constant use, environmental conditions, and mechanical loads. Welded steel, while incredibly durable, can be susceptible to corrosion, especially in humid or chemically exposed environments.
Rust and oxidation weaken steel over time, requiring protective coatings or treatments to maintain its integrity. Additionally, steel structures that endure continuous vibration or repetitive stress may develop fatigue cracks, making repairs more complicated.
Aluminum framing, in contrast, naturally resists corrosion, making it a superior choice for long-term durability in moisture-prone areas or cleanroom environments. Its ability to withstand repetitive motion without weakening makes it ideal for workstations that experience frequent adjustments or reconfigurations.
Unlike steel, aluminum doesn’t require coatings or extensive maintenance to prevent degradation, ensuring a longer-lasting, low-maintenance solution.
Repair and Replacement Options for Damaged Components
Accidents happen, and when a workstation frame gets damaged, the ability to repair or replace components quickly can minimize downtime. Welded steel frames pose a challenge when it comes to repairs.
Since the structure is welded together, fixing a damaged section often involves cutting and re-welding, which requires skilled labor and can be time-consuming. For workstations that need minimal interruptions, this can be a major drawback.
Aluminum framing, however, offers a modular design that simplifies repairs. If a section becomes damaged, it can be removed and replaced without affecting the entire structure.
The use of T-slot connections allows for easy disassembly, making adjustments quick and hassle-free. This flexibility reduces downtime and extends the life of the workstation without the need for extensive labor or specialized tools.
Weight Differences That Affect Mobility and Transportability
Weight plays a big role in how easily a workstation can be moved or reconfigured. Steel is significantly heavier than aluminum, making it a stable but less mobile option. Once installed, a welded steel workstation is typically a permanent fixture, requiring equipment like forklifts or cranes to relocate.
While this weight provides stability, it can also limit versatility, especially in workspaces that need to be restructured frequently.
Aluminum framing, being much lighter, is easier to transport and reposition. This makes it an excellent choice for dynamic work environments where layouts need to change based on production demands.
Workers can move and adjust aluminum-framed workstations without the need for heavy machinery, allowing for greater efficiency and adaptability. The reduced weight also lowers shipping costs when transporting pre-assembled or modular workstation components.
Integration with Automation and Ergonomic Adjustments
Modern workstations often incorporate automation, conveyor systems, and ergonomic adjustments to improve productivity and worker comfort. Welded steel structures, while sturdy, can be difficult to modify once installed.
Adding automation equipment or adjusting height requires extensive modifications, making it less ideal for workspaces that frequently adapt to new technology.
Aluminum framing excels in this area because of its modular nature. It allows for easy integration with automation components, conveyor attachments, and ergonomic adjustments such as height adjustability.
Accessories can be added or removed as needed, giving businesses the flexibility to evolve their workstations without major structural changes. The adaptability of aluminum framing makes it a preferred choice for companies that prioritize efficiency and worker comfort.
Expansion Capabilities Without the Need for Cutting or Welding
Growth and change are inevitable in manufacturing and industrial settings. The ability to expand a workstation without major reconstruction can save time and resources.
Welded steel structures, once in place, require cutting and welding to extend or modify, making expansion a labor-intensive process. Businesses that need scalable solutions may find this limitation a challenge as their needs evolve.
Aluminum framing eliminates this issue with its modular design. Extensions can be added without cutting, welding, or major modifications. New sections can be attached seamlessly, allowing for quick adjustments without disrupting workflow.
This makes aluminum framing an excellent long-term investment for companies that anticipate growth and need a workstation that can expand alongside their operations.